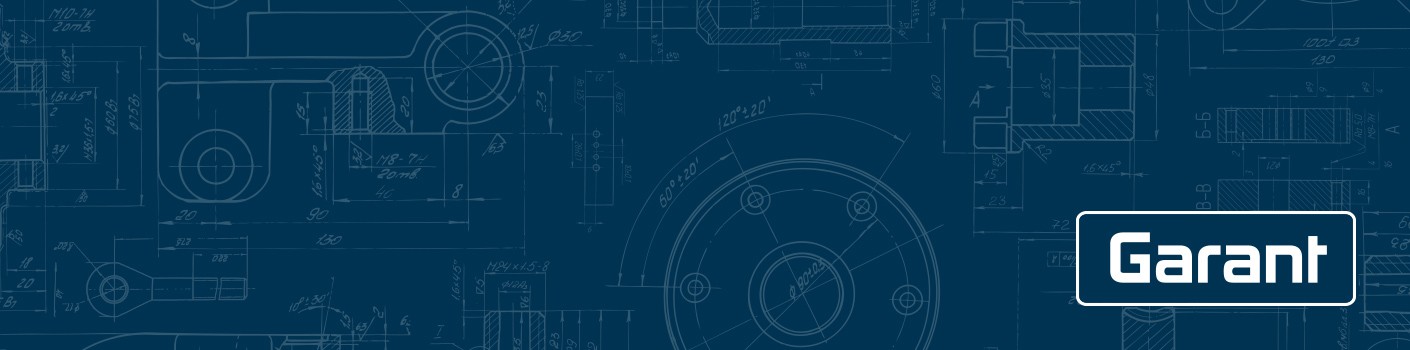
Professional milling cutter for machining titanium
GARANT Master Titan for highest process reliability and effiency
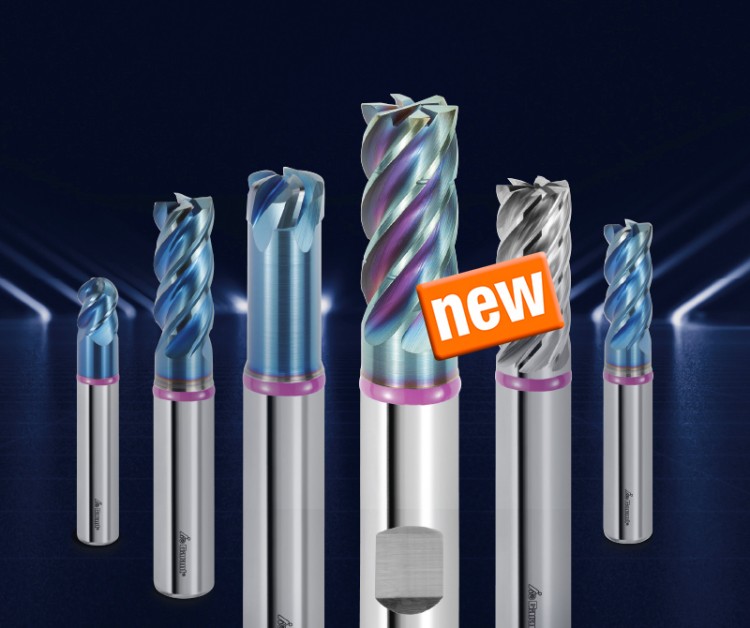
Die GARANT Master Titan family
Diversified portfolio:
13 specialised milling cutters for various applications in machining titanium provide the respective optimal solution.
Highest process reliability:
The TPC geometry significantly increases process reliability especially in automated production.
Superior tool life:
The GARANT Master Titan solid carbide roughing end mill HPC 203029 12 achieves a 30% longer tool life than the next best competitor.
GARANT Master Titan TPC
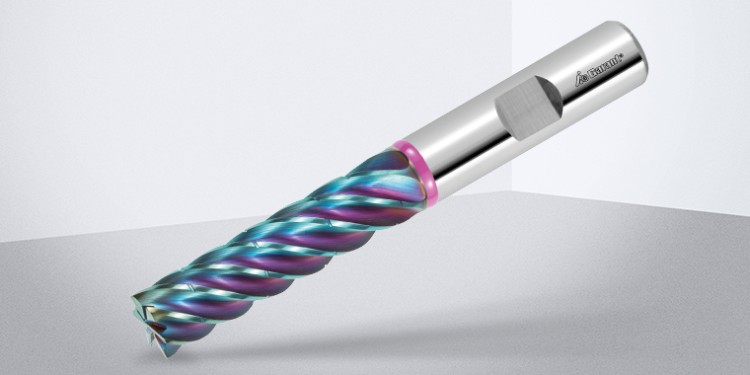
Even titanium materials can be machined using the TPC milling process.
The chips are broken into short lengths, thereby reducing the risk of chip accumulations to a minimum. Chip clogging is avoided. This significantly increases process reliability, especially in automated production!
Trochoidal Performance Cutting
- Very high metal removal rate especially when used on difficult-to-machine materials
- Very high dynamic path speed
- Very low cutting force
- Low wear
- High savings potential compared to the conventional strategy
Requirements for successful TPC machining
- A modern CAM system or modern machine control
- A machining centre with the most dynamic characteristics possible
- TPC tools from GARANT − specially developed for the requirements in trochoidal application
All advantages at a glace
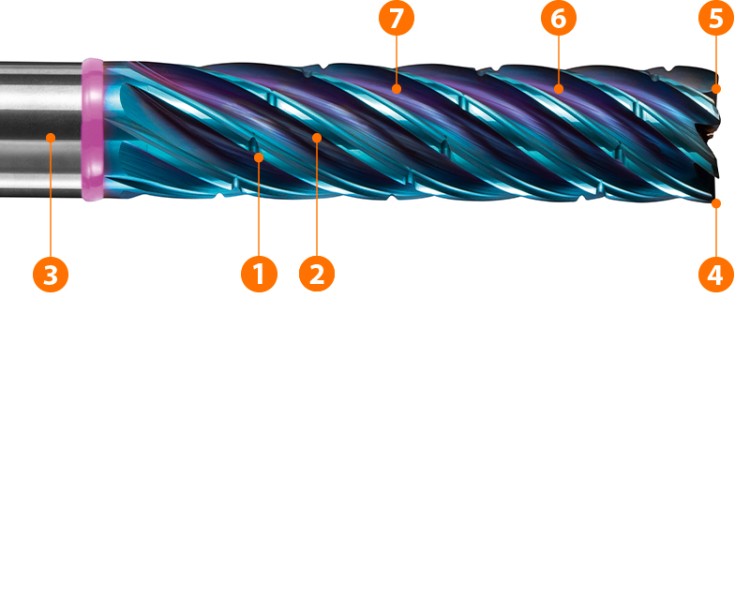
GARANT Master Titan TPC. More chip separators for shorter chips.
The chips are broken into short lengths, thereby reducing the risk of chip accumulations to a minimum.
- Innovative arrangement of chip breakers for short chips, to prevent accumulation of chips.
- Specially formed chip flutes neatly roll the chips up for quick and reliable evacuation.
- Strengthened core diameter for very high stability in TPC applications.
- 6 teeth for very high efficiency and feed rates.
- Selective cutting edge preparation, for very high process reliability.
- Consistently high-performance substrate within the entire Master Titan range.
- The familiar innovative coating of the Master Titan series for the best possible prevention of heat transfer into the tool.
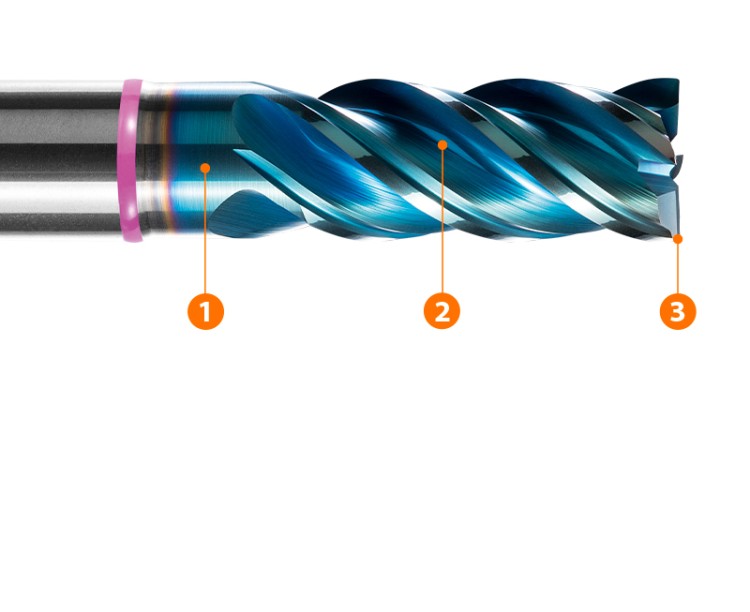
Master Titan solid carbide HPC roughing end mill. Immense chip volume thanks to high feed rates.
The coated solid carbide HPC roughing end mill is characterised by particular stability and long tool life.
- A stable core diameter avoids tool displacement.
- Polished chip flutes against formation of built-up edges.
- Honed cutting edges for edge protection.
Excellent emergency operating features.
The extremely efficient substrate is resistant to flexural breakage and its wear-resistance has been optimised.
An innovative coating prevents heat input.
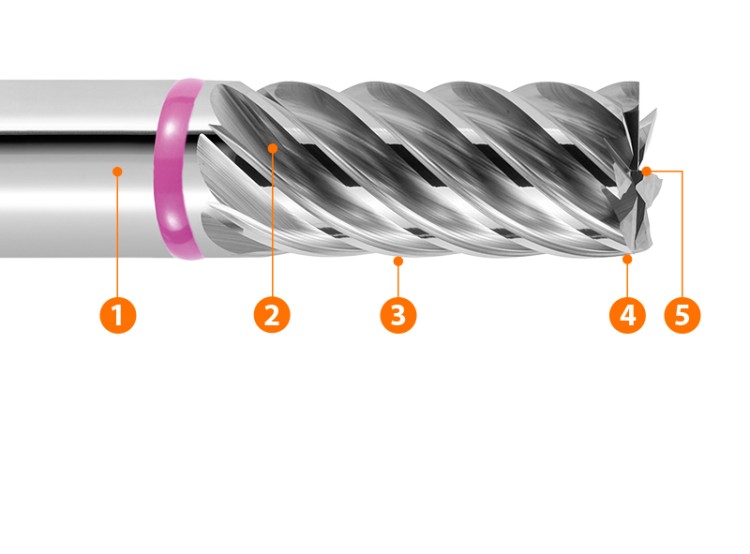
Master Titan solid carbide HPC finishing cutter. Maximum feed rates thanks to seven cutting edges.
The uncoated solid carbide HPC finishing cutter is used where the material must be kept absolutely free of
particles of coating material, for instance in medical technology applications.
- A stable core diameter prevents tool displacement.
- Polished chip flutes against formation of built-up edges.
- Selective cutting edge preparation for wear optimisation.
- Honed cutting edges for edge protection.
- 7 cutting edges for especially high efficiency.
Master titan compared to the competition
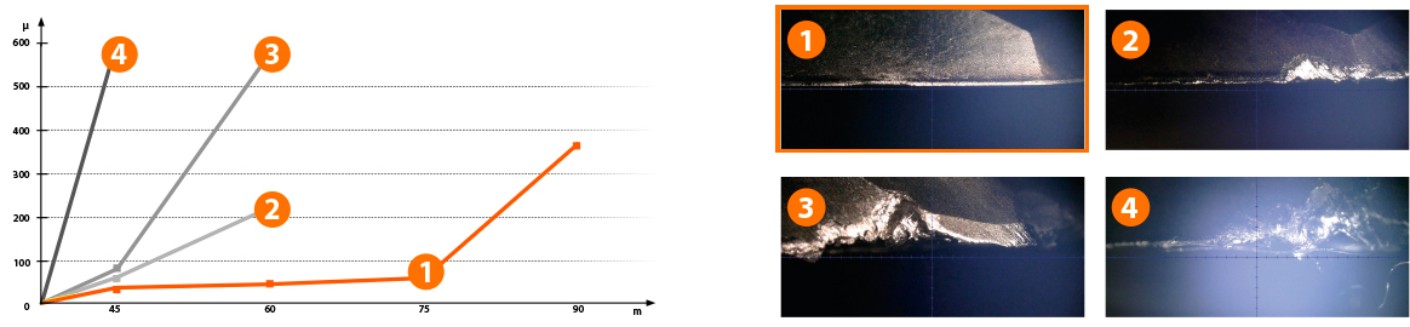
The GARANT Master Titan solid carbide roughing end mill HPC 203029 12 took on the competition and won – across the board!
The GARANT Master Titan (1) showed cutting edge wear only after 75m, the competition already at 45m (2,3).
Set-up of the test: Multi-pass machining of a workpiece: Material 3.7165 (Ti6Al4V).
Cutting data: vc = 60 m/min, fz = 0.07 mm, ae= 4.8 mm, ap= 12 mm, with cooling/emulsion, diameter milling cutter 12 mm, number of cutting edges 4
Titanum - a material with special characteristics

- The high strength of titanium (Ti) results in a costly and energy-intensive production process, which is around 25 times more expensive than that of high-quality alloy steels.
- Titanium has a lower thermal conductivity than aluminium (Al).
- A large proportion of the process heat is transferred to the tool cutters, resulting in a high wear rate.
- The heat resulting from aluminium processing is dissipated via the swarf and the wear on the tool is reduced.
- Compared to aluminium, a very soft material, titanium is difficult to mill / turn due to work hardening.
- The tendency to seize due to the combination of elasticity and tensile strength poses a thread to taps.
- Processing of titanium also requires sufficient cooling as the resulting chips are highly flammable.