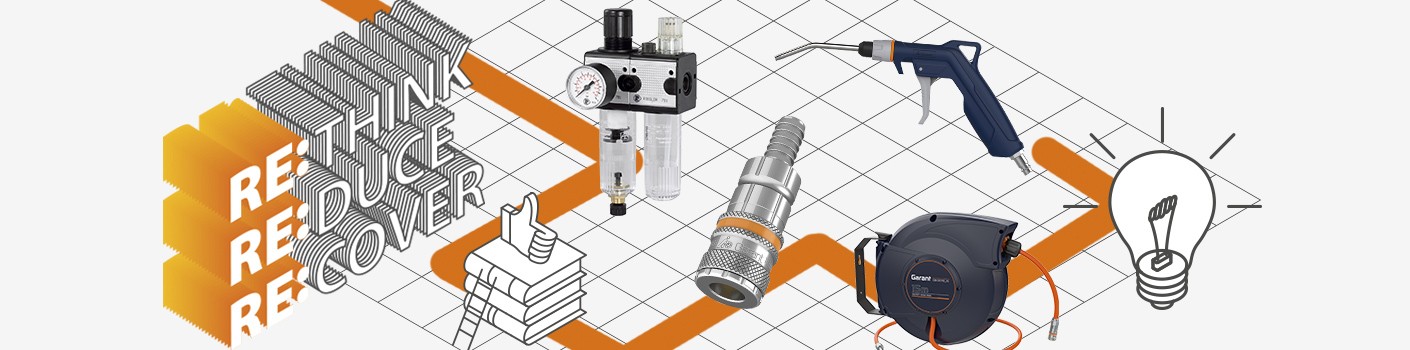
Work correctly with pressure without feeling the pressure – how to make energy savings when using compressed air
Discover how the efficient use of compressed air can save you money
Did you know that German industrial companies need around 16 terawatt-hours of power each year to generate compressed air? This figure, as calculated by the German Energy Agency dena, is enormous but it comes as no surprise when you consider that compressed air is indispensable for 90 percent of industrial processes. Whether it’s blowing components clear, drying, cooling, suctioning, cleaning, sealing, ionising or transporting – compressed air is one of our most important resources. However, it’s also a major factor affecting energy costs. That’s why it’s worthwhile taking a closer look at your consumption of compressed air to see where you can save energy.
The biggest compressed-air losses occur on the way to the application itself
Did you know that up to 50% of the compressed air generated is wasted by using compressed-air systems that are not, or only poorly, optimised? Although pressure loss is a well-known issue, a study conducted by the European Commission revealed that only 9% of respondents investigate the causes of excessive compressed-air consumption. 75% indicated they lacked the necessary expertise to do so. Our mission is to change this, as the reasons behind an unnecessary loss of compressed air are relatively simple to find.
This article focuses on how to optimise your compressed-air components, provides information on how to identify leakages and helps you when choosing which tool is best for you. After all, we must remember that the unnecessary costs do not occur where the air is supplied, but on the way to the application itself.
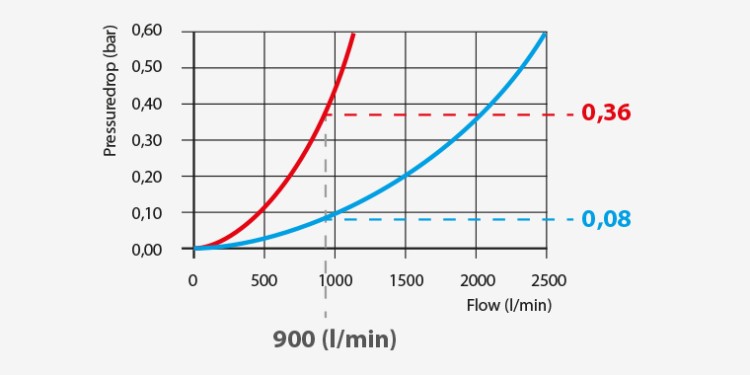
A drop in pressure significantly reduces efficiency
Pneumatic tools are designed for a certain working pressure, usually 6.3 bar. This is assumed to be dynamic pressure which is set when the valves are open. It is always slightly lower than the static operating pressure that is read off on the pressure gauge with a closed valve. If the pressure drops, the compressor output is significantly reduced. As such, it often seems obvious to start looking for the problem on the compressor. However, what you should do instead is check the compressed-air components first, particularly the connection points.
How much compressed air are you using?
Do you need to rethink your consumption of compressed air? This is true for eight in every nine companies. Take the time to take stock and see where your company is at. Now is the perfect time to do it, as any unnecessary wastage of compressed air will be felt all the more acutely in the current energy crisis. The following table provides an example of how rising energy prices can have an additional impact on your costs.
In order to calculate your actual compressed-air costs, we recommend obtaining expert advice from professionals or specialist companies. We would then be pleased to advise you on which compressed-air components or tools would be the right ones for you.
How to prevent high follow-on costs
It’s not just an unnecessary loss of compressed air that you have to bear in mind – incorrectly sized compressors or compressors that run for too long also cause costs to skyrocket.
If you’ve noticed that your work time per unit produced increases when using compressed air, it’s time to take action. If you fail to do so, the costs of all stages involving the generation of pressure will also increase, potentially amounting to several tens, of not hundreds, of thousands of euros each year. This is exacerbated by higher maintenance costs and the costs of purchasing new tools as a result of the increased stress placed on the tool and compressor.
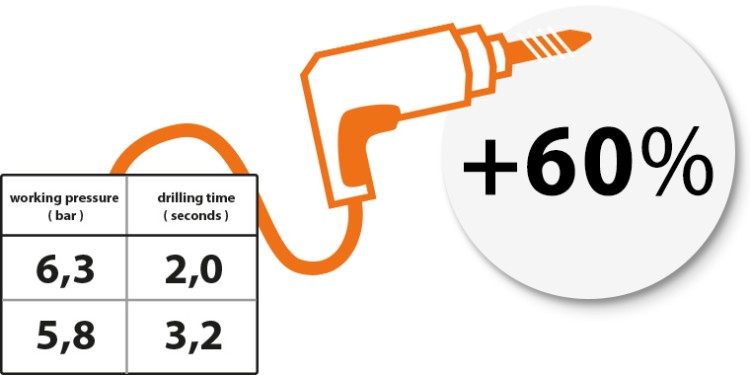
The key to making savings using a drilling machine by way of example
If we look at a drilling machine by way of example we can see what impact an insufficient dynamic pressure at the tapping point has on the overall costs. If the compressed air were to fall by just 0.5 bar, the drilling time alone will increase by some 60%! This would cause increased costs of more than 240 euros a month. Unfortunately, this example is commonly found in most companies.
Your step-by-step guide to reducing pressure losses
Step 1: Identify the main cause of leakages
Check your compressed-air system regularly for leakages. Start with any connected accessories. We show you the steps you can take.
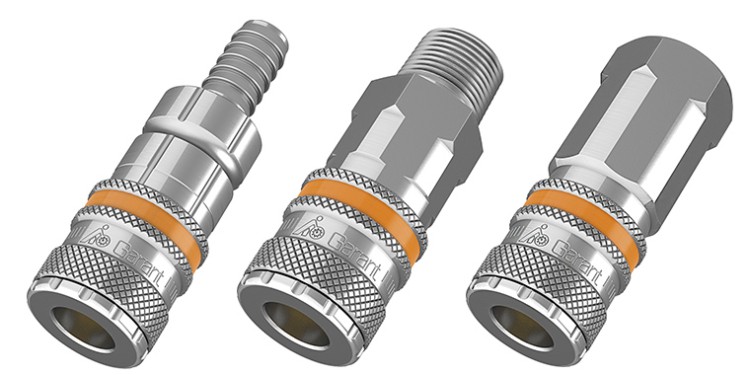
Couplings
70 to 80 percent of leakages can be traced back to sub-optimal use of couplings. Generally speaking every coupling is a potential source of pressure loss, so it’s important to carefully consider how many couplings to use and when to use them. Of course, sometimes you just can’t do without them. Whether or not you need a coupling depends on things like how often you want to change the tool. If the couplings are exposed to strong vibrations (as is the case with impact wrenches and chisel hammers), we recommend using a short hose (0.3 to 0.7 metres) before the main hose.
Make sure to replace old couplings, as old, self-bleeding quick-change couplings made of brass are particular problem spots when it comes to compressed air. This is because they have a ball located in the air flow. Modern quick-change couplings drastically reduce losses (to around 0.2 bar), meaning they pay for themselves very quickly. Practical experience has shown that switching to modern, perfectly adjusted couplings enables you to save up to 240 working minutes a day (source: cejn.com). Our video clearly explains how the choice of coupling affects the flow of compressed air, using the HOLEX industrial quick-change coupling by way of example.
Step 2: Measuring and adjusting the dynamic pressure
After optimising the surrounding components, the tool working pressure will probably still be too high. You can reduce it using the rotary knob on the service unit. Flowmeters can be connected to all compressed-air systems.
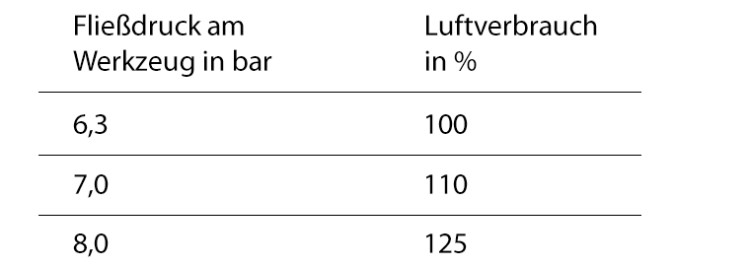
If the pressure drops below 2 bar, air consumption will increase by 25 percent. It will be in the ideal range at 6.3 bar.
Step 3: Make sure to select a high-quality tool
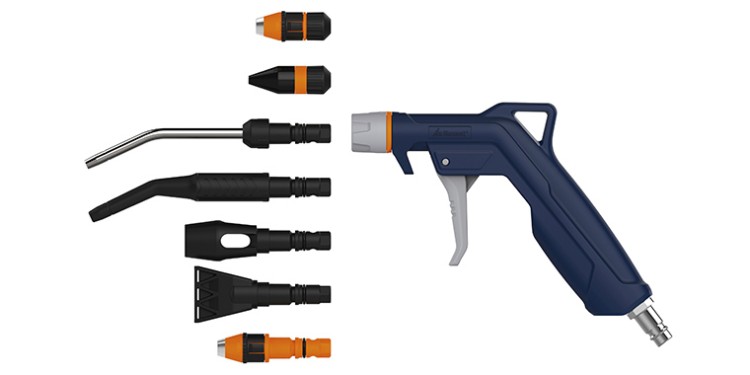
The last link in the compressed-air chain is the pneumatic tool itself. Don’t take any chances here – look for a top-quality, durable tool. After all, a chain is only ever as strong as its weakest link. Choosing the correct tools is always worth it and will bring lasting benefits. Our network of technical advisers and application technicians would be glad to help you choose the right tool for you and the appropriate compressed-air components. It is important to choose the right dimensions and settings and service them well, otherwise your productivity will drop drastically.
Tip: Using consistent components, i.e. compressed-air components from one system, will give you the best-possible tool set-up.
Step 4: Invest in a service unit
Step 5: Ensure safety at work
In a nutshell: Work correctly with pressure without feeling the pressure.